technology
02 Casting
Isoda Metal is manufacturing two different types of bearings; types to cast copper alloy and to cast white metal on the inner surface of bearing. In this casting process, the alloy is adhered to inside of the back-metal (steel) as the base. When we manufacture bearings, mainly two different types of casting method are employed. One is the centrifugal casting. In this method, melt alloy is casted into the back-metal that is heated at a high temperature and is rotated at a high speed. By utilizing the centrifugal force, two different metals are adhered (welded) elaborately. To produce highly sophisticated bearings, technologies based on knowledge, experience and equipment that have been accumulated for a long period are necessary, including temperature and combination of back-metal and alloy, centrifugal force when the back-metal is rotated and others. The other method is the gravity casting that melted alloy is poured into the inner side of a fixed back-metal. Unlike the centrifugal casting, there is no high speed rotation, but the centrifugal casting and the gravity casting are the same in aspect that the adherence level is increased when the heated back-metal at a high temperature is welded to the melted alloy. In order to firmly adhere the alloy to inner surface of the back-metal, temperature control for both sides is critical. Size and shape of bearings as well as composition and thickness of the suitable alloy differ depending on the size and output of the engine to be used. Accordingly, it is necessary to select the best suited casting method and alloy type for the required conditions of each product. To produce highly reliable products, it is necessary to consider the temperature control appropriate to the material as well as speed and direction of the centrifugal force and cooling speed.
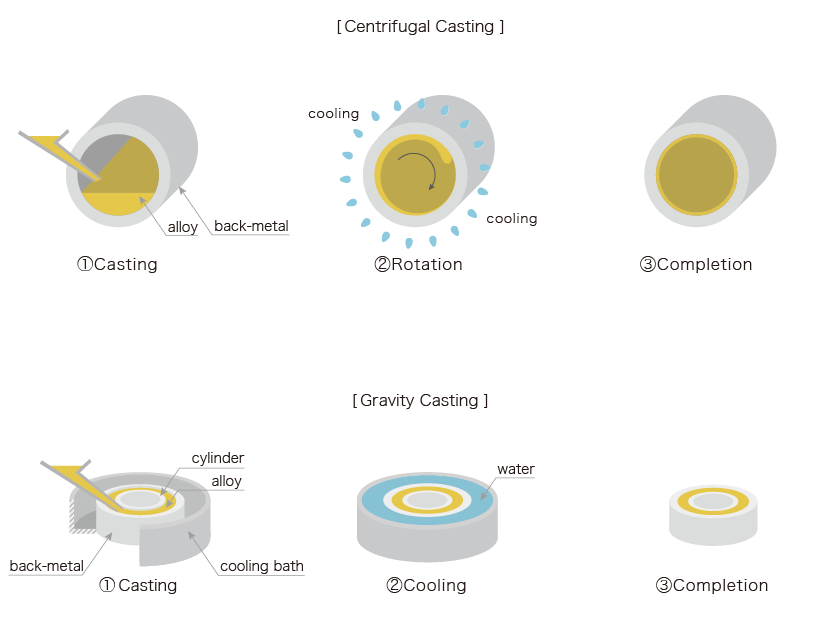
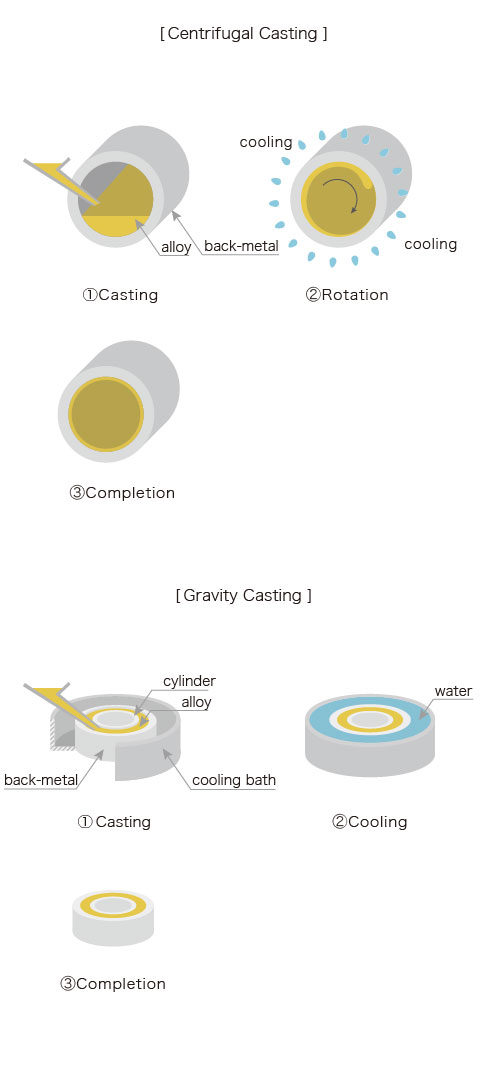
